Thermal Validation
Thermal validation is the process of verifying and documenting that a temperature-controlled environment, such as an incubator, oven, or freezer, meets the required temperature standards for its intended use. Thermal validation is a critical process in various industries, including pharmaceuticals, biotechnology, and food manufacturing, where temperature control is essential to maintain product quality and safety.
Thermal validation typically involves placing temperature sensors in the environment being validated and monitoring the temperature over a period of time. The temperature data is then analyzed to determine whether the environment is operating within the required temperature range and meets the required standards. Thermal validation may also involve the calibration of temperature sensors and the verification of the temperature control system's accuracy.
The results of thermal validation are typically documented in a report, which provides evidence that the temperature-controlled environment meets the required temperature standards. This report is used to demonstrate compliance with applicable regulations and standards and to ensure product quality and safety.
Qualification in following Equipments:
Thermal validation cycle for CSV and PLC validation as per GAMP 5:
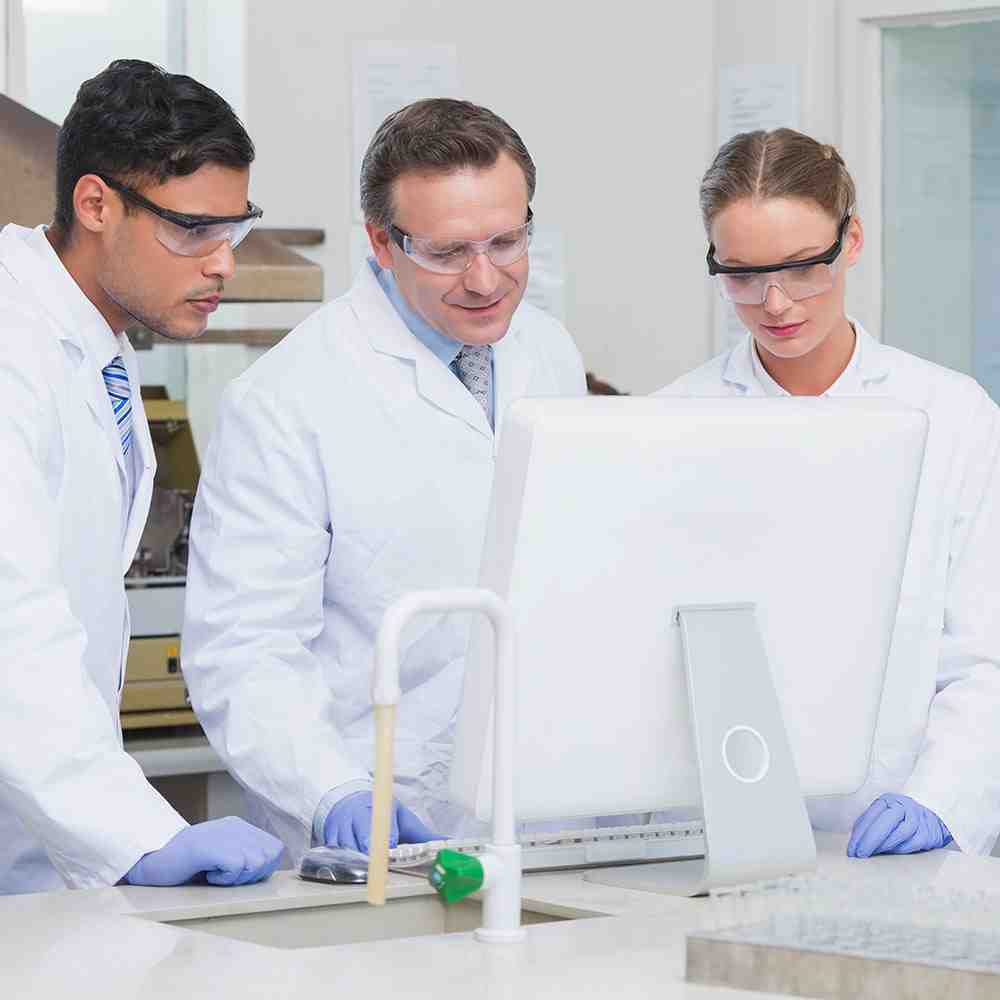
01. Plan and Prepare:
The first step is to plan the thermal mapping process, which involves identifying the areas to be mapped, selecting the appropriate sensors, and determining the duration of the mapping process. The thermal mapping plan should also specify the acceptance criteria, which define the allowable temperature range for the environment being mapped. Once the plan is established, the sensors are selected and placed in the designated areas.
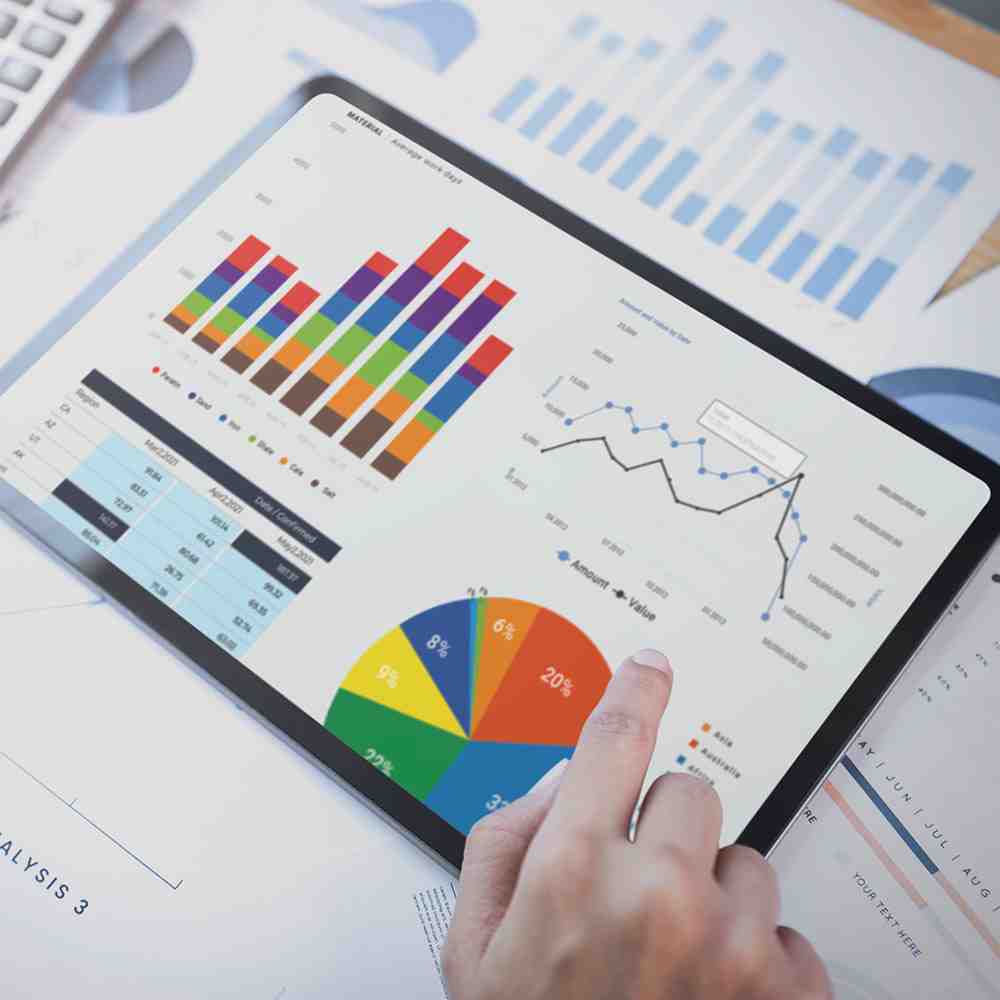
02. Data Collection:
The next step is to collect temperature data from the sensors. The data collection process typically involves running the temperature-controlled environment through a representative operating cycle, which may include ramp-up, hold, and cool-down phases. During this time, the sensors record the temperature and Humidity at specific intervals.
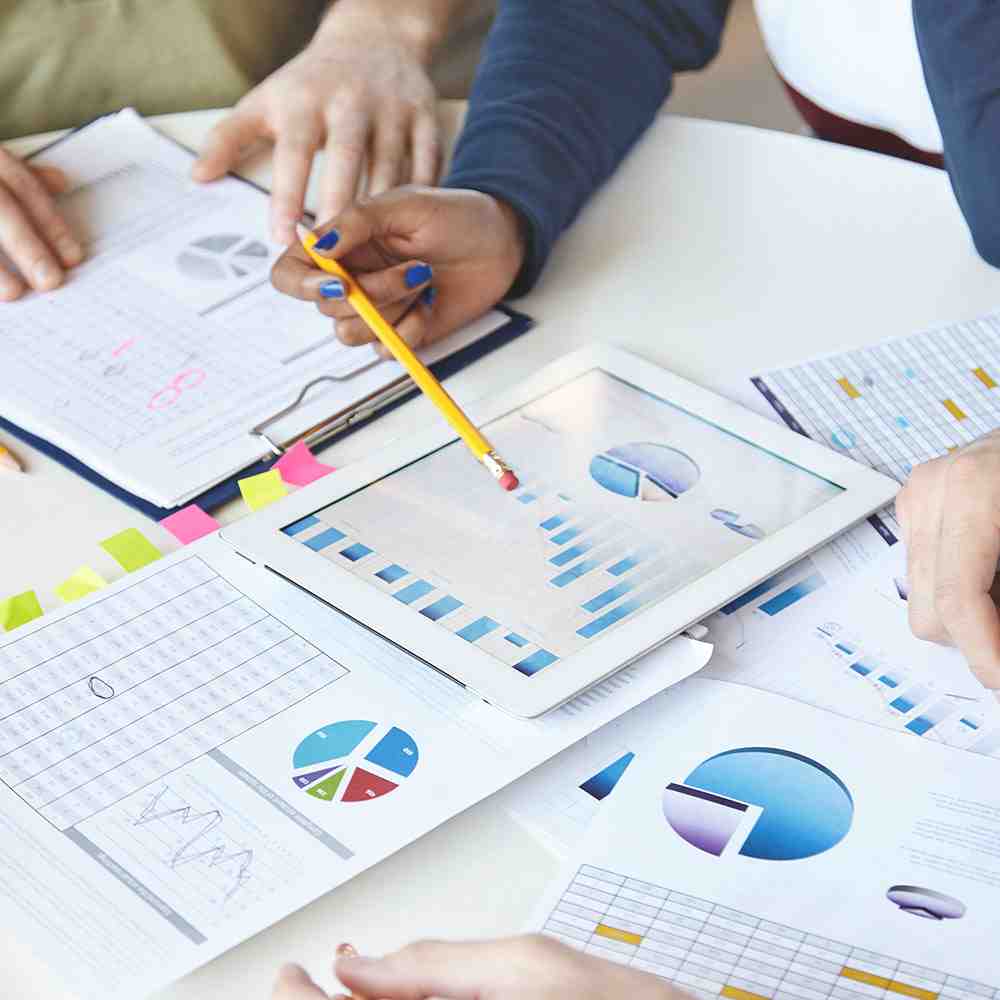
03. Data Analysis:
Once the data is collected, it is analyzed to determine the temperature distribution within the temperature-controlled environment. The data analysis process involves creating a temperature & RH map that displays the temperature & RH at various locations within the environment. The temperature & RHmap is then compared against the acceptance criteria established in the planning phase to determine whether the environment meets the required standards.
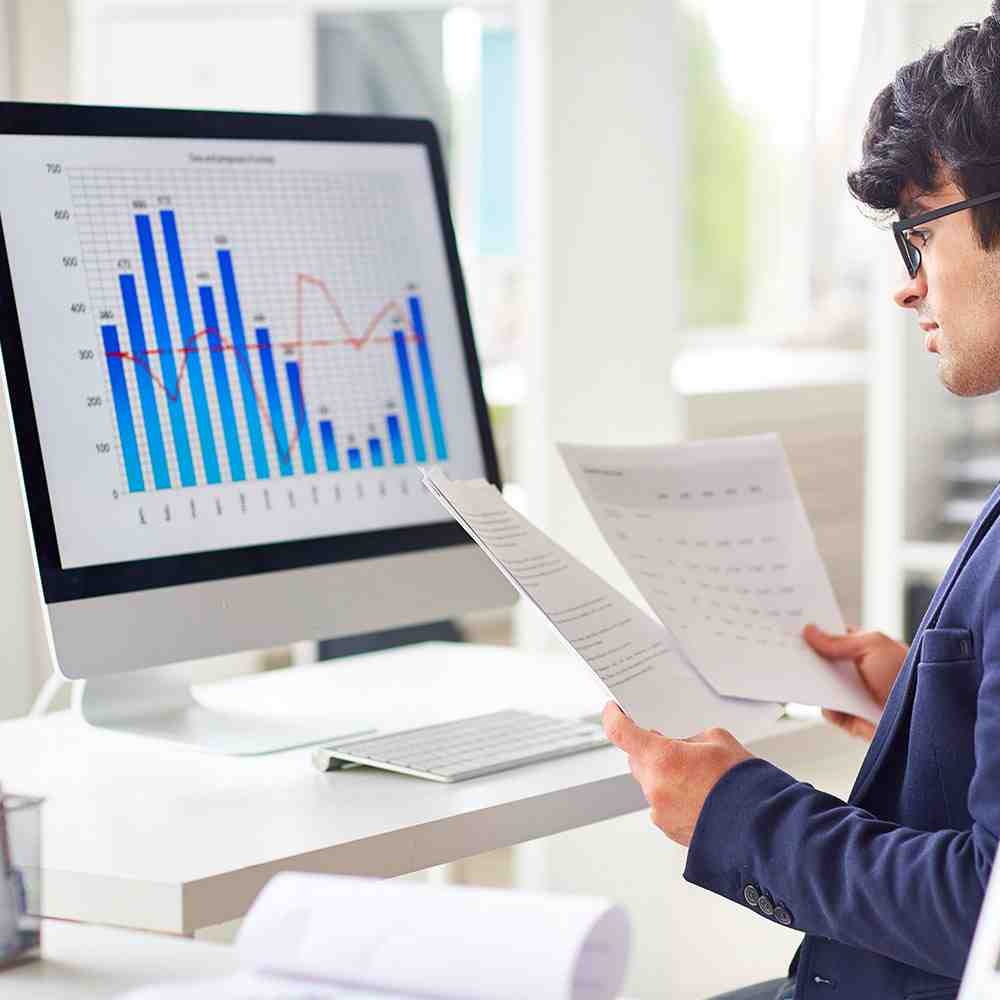
04. Report Generation:
Finally, a report is generated that summarizes the results of the thermal mapping process. The report typically includes the temperature map, a summary of the data analysis, and any corrective actions taken if the environment did not meet the required standards. The report provides evidence that the temperature-controlled environment meets the required temperature standards and ensures that products produced within the environment are of high quality and safe for consumption or use.